If you're not an installer, and you're in the process of specifying a resilient floor, here's what you need to know about heat welding vs chemical welding techniques. You know all too well that the floor plays a big role in the overall appearance, functionality and safety of the facility and each cut, seam, and weld matter, so choosing the right technique is critical for the overall success of your flooring choice.
As a manufacturer of resilient flooring for more than 100 years, here at Mannington Commercial we’ve crafted a variety of flooring options to meet a variety of needs, and we want to help you choose which type of welding to create a seamless resilient flooring and having an integral surface.
In this article, we’ll tackle two main types of welding used in flooring installation:
Heat Welding
Heat welding is marrying two pieces of flooring together with heat and a welding rod. To heat weld sheet vinyl, you first install the flooring to the manufacturer’s specifications, using the recommended adhesive. It’s important to follow the instructions with regard to the adhesive, usually followed by a waiting period of at least 24 hours before any heat can be applied to the flooring. This is because the heat of the welding process can affect the adhesive under the surface, rendering your installation flawed. Once the waiting period is up, the installer will route out both edges of the flooring material where they meet approximately two-thirds the depth of the flooring, careful not to route all the way through the product. At this point, a welding rod of coordinating (or contrasting) material is used with heat welding tools to weld the two edges together. This technique will create what is referred to as a heat welded seam.
Again, there is a waiting period for the seam to cool. Afterward, a skilled installer will remove the excess material created in the welding process. This process can be described as tedious and requires skill being careful not to damage the surface of the surrounding flooring. Knowing how to avoid pitfalls such as scorching (which compromises the finish of the flooring) or cold spots (where the groove is not fully bonded) is critical. While heat welding is a straightforward process, it requires a great deal of practice, precision and the proper tools, which can be quite costly!
So you may be wondering why you would choose heat welding if it is costly, time-consuming and requires expensive tools and expert installers. Heat welding is often specified for installations where bacteria or other pathogens are a concern, such as healthcare environments. The “seamless”/integral nature of heat welding prevents joints where bacteria or pathogens can collect, giving you a more sterile environment.
Heat welds are widely used in hospitals and other healthcare facilities because it can hermetically seal sheet vinyl in sterile operating rooms, critical-care patient spaces and laboratories.
Related: Sheet Vinyl vs. Luxury Vinyl Tile: Best Flooring For Infection Control
To learn more about Heat Welding watch the video below:
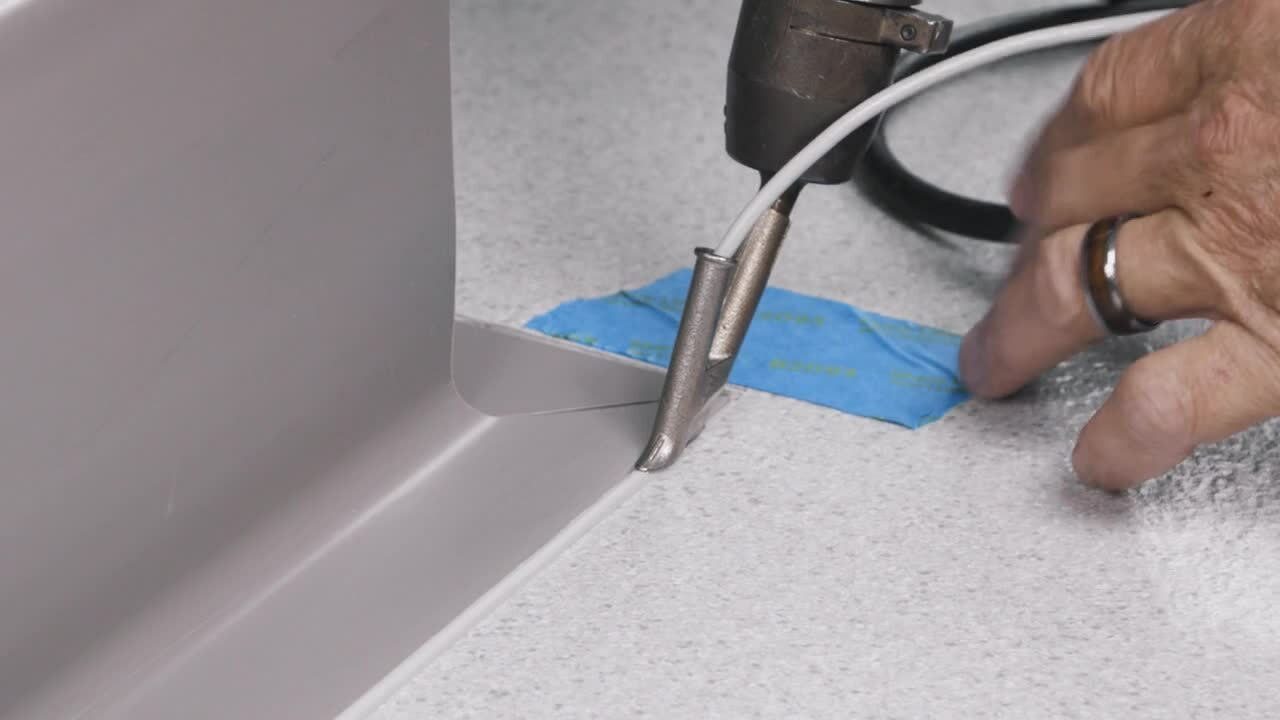
Chemical Welding
A chemical weld is another way of fusing two pieces of vinyl flooring together to provide a seamless or integral appearance. The weld is actually a chemical reaction in which the weld is created by liquid. The process of the sealer dissolving and melting the vinyl together is similar to the process used to seal two vinyl pipes together in plumbing applications. Because there is no routing involved, chemical welding is often chosen for aesthetic reasons. A chemical weld generally creates a less obvious seam than a routed heat weld.
In order to chemically weld two pieces of flooring, both pieces must be touching one another after installation. It needs to be a comfortable fit, meaning not too tight or too loose.
The flooring needs to be installed to the manufacturer’s specifications, using the appropriate adhesive and making sure the edges are clean. There should not be any residual dirt, adhesive or other substance that might show in the finished seam. The manufacturer may recommend a wait time on the adhesive before chemical welding, but because chemical welding does not use heat to fuse the flooring together, there is less risk of affecting the adhesive as there is in heat welding so chemical welding can typically be completed faster than heat welding.
When using chemical welding, an installer forces the applicator tip of the chemical liquid between the two pieces of flooring and squeezes a clear liquid between the two pieces of flooring. As the liquid sits between the two pieces, it causes a chemical reaction that fuses the two pieces together. With this method, there are no special tools required above and beyond normal sheet vinyl installation tools that an installer of sheet vinyl would have and be trained to use other than an under-scribing tool that is set correctly to give you that nearly invisible finish that a chemical weld can provide.
The biggest risk to a chemical weld is applying the correct amount of sealer: applying too much floods the surface whereas too little can create a weak weld. Because the sealer is clear, sometimes it is difficult to tell how much has been applied.
A chemical weld is best used in areas where light to normal traffic is anticipated, not generally applicable for areas of very heavy foot traffic or constant rolling loads. Also, it is best used where the area is not exposed to constant excessive topical moisture.
Now that you know the difference between heat welding and chemical welding, you can choose the right technique to make your space a success.
Would you like to learn more about resilient flooring while earning AIA/IDCEC CEU credits? We have a CEU for you.